Comprehending Porosity in Welding: Exploring Reasons, Effects, and Prevention Strategies
As professionals in the welding sector are well mindful, comprehending the reasons, results, and avoidance techniques associated to porosity is crucial for accomplishing robust and trustworthy welds. By diving right into the origin causes of porosity, examining its detrimental impacts on weld high quality, and discovering effective avoidance approaches, welders can improve their expertise and skills to create premium welds regularly.
Typical Sources Of Porosity
Contamination, in the kind of dirt, grease, or rust on the welding surface area, creates gas pockets when heated, leading to porosity in the weld. Inappropriate securing takes place when the shielding gas, generally made use of in procedures like MIG and TIG welding, is incapable to completely secure the liquified weld swimming pool from responding with the surrounding air, resulting in gas entrapment and subsequent porosity. Furthermore, insufficient gas insurance coverage, often due to incorrect circulation rates or nozzle positioning, can leave parts of the weld vulnerable, permitting porosity to form.
Effects on Weld Top Quality
The visibility of porosity in a weld can substantially endanger the general quality and integrity of the welded joint. Porosity within a weld creates gaps or tooth cavities that compromise the framework, making it much more prone to splitting, deterioration, and mechanical failing. These spaces act as stress concentrators, minimizing the load-bearing capability of the weld and enhancing the possibility of early failing under applied stress. In addition, porosity can additionally act as possible websites for hydrogen entrapment, further intensifying the destruction of the weld's mechanical buildings.
Additionally, porosity can hinder the effectiveness of non-destructive screening (NDT) techniques, making it challenging to detect various other issues or stoppages within the weld. This can bring about substantial security worries, particularly in important applications where the structural stability of the bonded elements is vital.

Prevention Techniques Overview
Provided the harmful effect of porosity on weld top quality, efficient avoidance methods are critical to maintaining the architectural integrity of welded joints. Furthermore, selecting the ideal welding specifications, such as voltage, current, and take a trip rate, can aid lessen the threat of porosity development. By integrating these prevention techniques into welding practices, the event of porosity can be substantially reduced, leading to more powerful and more dependable bonded joints.
Significance of Appropriate Protecting
Proper shielding in welding plays an important role in protecting against climatic contamination and making certain the honesty of welded joints. Shielding gases, such as argon, helium, or a blend of both, are typically made use of to find more protect the weld pool from responding with elements airborne like oxygen and nitrogen. When these responsive components come into contact with the warm weld swimming pool, they can create porosity, leading to weak welds with lowered mechanical buildings.

Poor shielding can lead to various issues like porosity, spatter, and oxidation, jeopardizing the structural integrity of the welded joint. Sticking to proper protecting methods is crucial to produce top quality welds with very little defects and ensure the long life and reliability of the welded elements.
Monitoring and Control Methods
How can welders properly keep an eye on and control the welding procedure to make certain optimal outcomes and stop problems like porosity? By continuously checking these variables, welders can recognize discrepancies from the perfect problems and make prompt modifications to protect against porosity development.

Furthermore, carrying out correct training programs for welders is necessary for keeping an eye on and controlling the welding procedure efficiently. What is Porosity. Informing welders on the significance of maintaining regular criteria, such as correct gas protecting and take a trip speed, can assist stop porosity concerns. Normal assessments and certifications can additionally ensure that welders excel in surveillance and managing welding procedures
Moreover, using automated welding systems can boost tracking and control capabilities. These systems can specifically regulate welding parameters, reducing the possibility of human error and making certain more consistent weld top quality. By incorporating advanced surveillance modern technologies, training programs, and automated systems, welders can effectively keep track of and manage the welding procedure to decrease porosity defects and attain top notch welds.
Conclusion
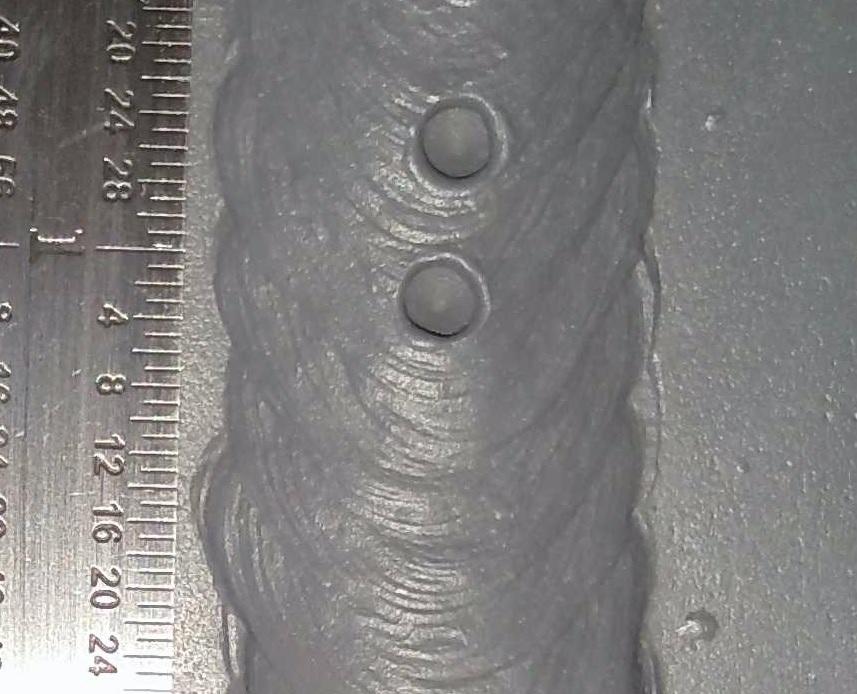